CHAVEZ
Well-known member
Dear Colleage:
Hi everybody, I have a problem with a Heidelberg Prosetter 52, the dot is distorted and suddenly lose the "synchrony" only in the data area, and the image is blur and the plate of course is unusable. The equipment never send any error message.
I am using the follow items:
Prosetter 52
User Interfaz version: 8.7
Windows 7 running on DELL Computer
Xitron Harlequin RIP Version 9.x with blue box interface
I appreciate your support, I tried get help from Xitron but they did not response.
Jose Chavez
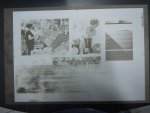
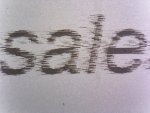
Hi everybody, I have a problem with a Heidelberg Prosetter 52, the dot is distorted and suddenly lose the "synchrony" only in the data area, and the image is blur and the plate of course is unusable. The equipment never send any error message.
I am using the follow items:
Prosetter 52
User Interfaz version: 8.7
Windows 7 running on DELL Computer
Xitron Harlequin RIP Version 9.x with blue box interface
I appreciate your support, I tried get help from Xitron but they did not response.
Jose Chavez
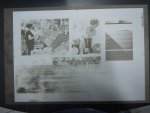
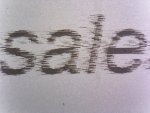