veronika_zoobs
New member
Hello all,
lurker for a few months, thanks for all the information you've given me thus far!
I work for a plastic die-cut card company and we digitally print on two Xerox 700's.
Aside from plastic cards, we also run paper cards which include postcards and such.
We have a great deal of problems trying to print large coverage areas with light colors.
I already know that large coverage areas pose issues for digital machines (experience) but we get great coverage on 100% Cyan (0% MYK) it's a nice, even coat on the paper. Our issue is with light colors over a large area, you can see streaks all up and down the sheet.
From left to right, 4 sheets:
1. Original print (not copied or scanned)
2. PMS 326 (to see if any change)
3. PMS 325
4. Changed the Cyan up a little in percentage, still streaked
Machine is set to 257-300 gsm, coated, on 13x19 sheets of 120 lb gloss cover (326 gsm).
Our problem may be that the paper is too thick for the machine, so we ran the same color on thinner stock.
We changed our template around to be able to print on 12x18 sheets of 300gsm coated cover, which fits the specifications of the machine, and the print at PMS 325 came out as so:
Other than replacing the developer and drums, toner cartridges, resets and calibrations (ALL DONE!), is there anything ELSE we can do to minimize the streaking in light colors??
lurker for a few months, thanks for all the information you've given me thus far!
I work for a plastic die-cut card company and we digitally print on two Xerox 700's.
Aside from plastic cards, we also run paper cards which include postcards and such.
We have a great deal of problems trying to print large coverage areas with light colors.
I already know that large coverage areas pose issues for digital machines (experience) but we get great coverage on 100% Cyan (0% MYK) it's a nice, even coat on the paper. Our issue is with light colors over a large area, you can see streaks all up and down the sheet.
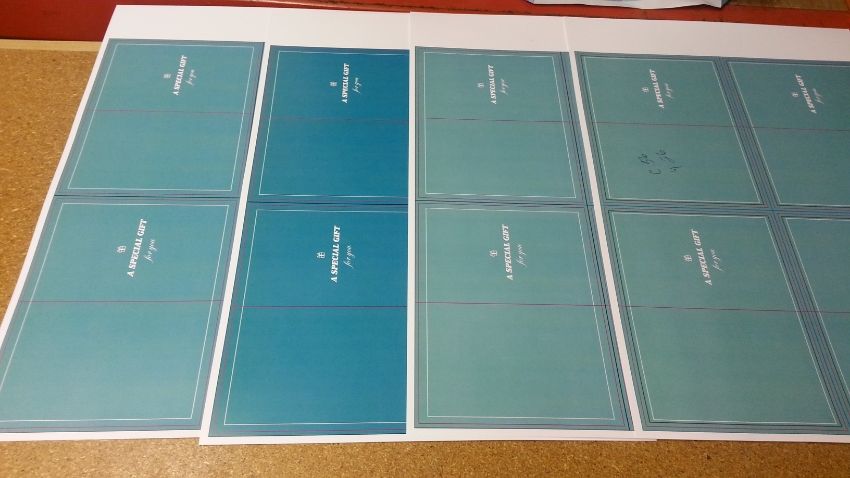
From left to right, 4 sheets:
1. Original print (not copied or scanned)
2. PMS 326 (to see if any change)
3. PMS 325
4. Changed the Cyan up a little in percentage, still streaked
Machine is set to 257-300 gsm, coated, on 13x19 sheets of 120 lb gloss cover (326 gsm).
Our problem may be that the paper is too thick for the machine, so we ran the same color on thinner stock.
We changed our template around to be able to print on 12x18 sheets of 300gsm coated cover, which fits the specifications of the machine, and the print at PMS 325 came out as so:
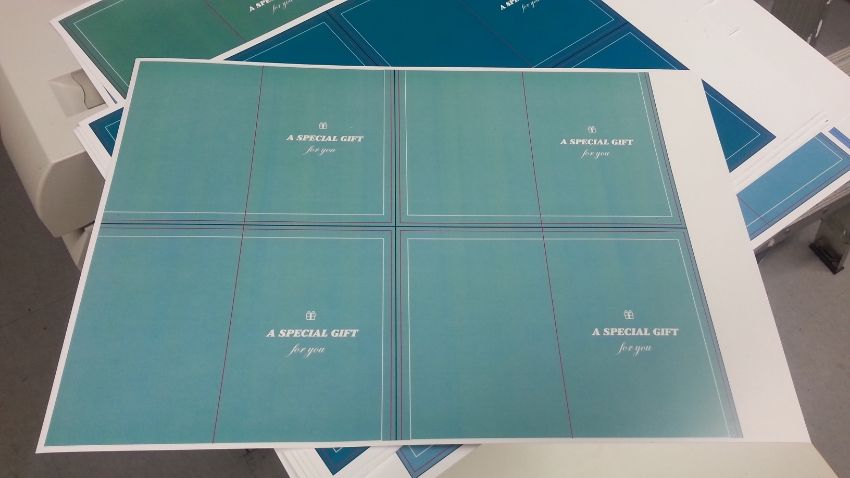
Other than replacing the developer and drums, toner cartridges, resets and calibrations (ALL DONE!), is there anything ELSE we can do to minimize the streaking in light colors??